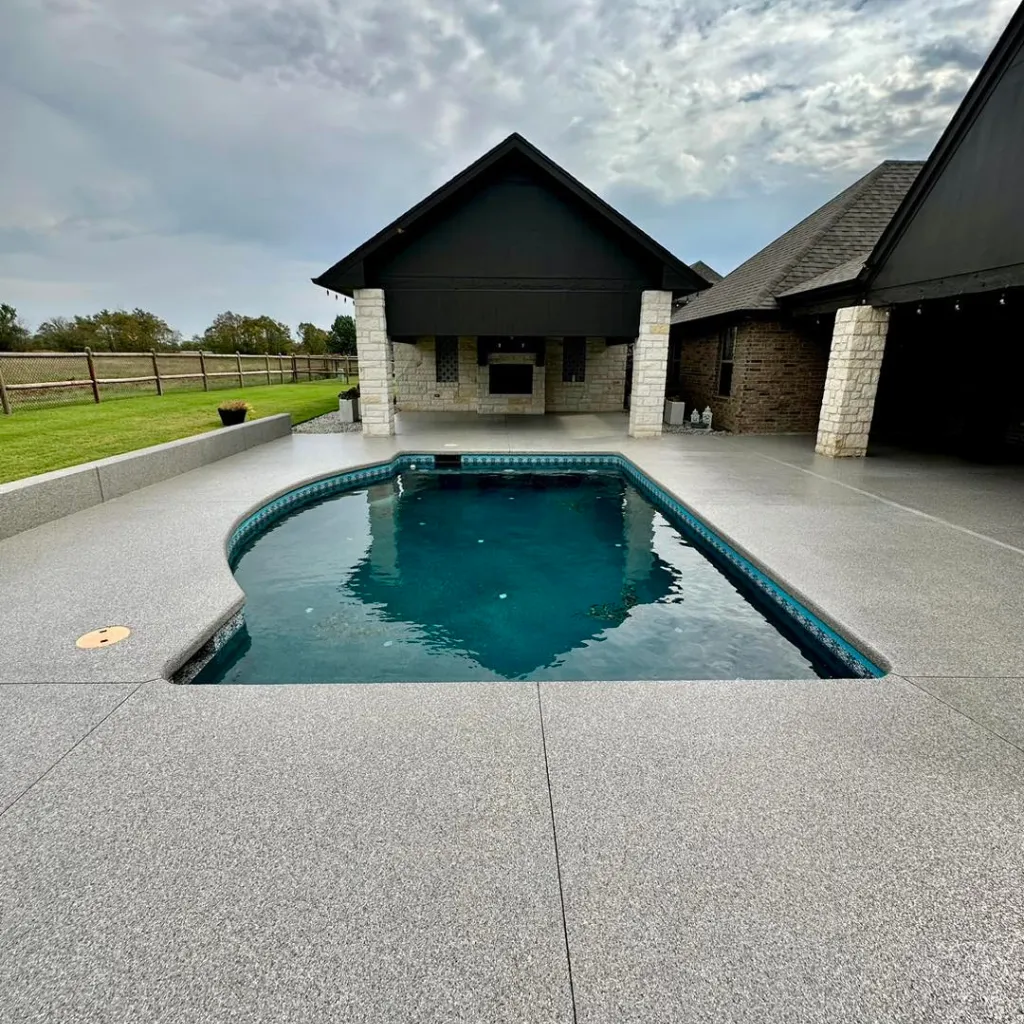
What's the Best Garage Floor Coating for Texas Weather?
What's the Best Garage Floor Coating for Texas Weather?
Why Texas Weather Creates Unique Challenges for Garage Floors
The Moisture and Humidity Challenge
Comparing Popular Garage Floor Coatings in Texas Conditions
1. DIY Epoxy Kits (The Texas Test Failure)
2. Professional Standard Epoxy Systems (The Compromise Option)
3. Polyurea Coating Systems (The Texas Weather Champion)
4. Hybrid Polyaspartic Systems (The Speed Champion)
5. Tile Systems (The Modular Option)
The Clear Winner for Texas Garages: Polyurea Coating Systems
1. Formulated for Extreme Conditions
2. Flexibility Matches Texas Soil Reality
3. Rapid Installation Reduces Weather Variables
4. Superior Heat Resistance for Texas Summers
5. Lifespan Economics Make Sense
Real Texas Customer Examples: Coating Performance in Action
The North Dallas Hot Tire Test
The Southlake Soil Movement Challenge
How to Choose the Right System for Your Texas Garage
Assess Your Concrete Condition
Factor in Your Local Microclimate
Why Professional Installation Matters Even More in Texas
2. Diamond Grinding vs. Acid Etching
3. Texas-Specific Product Selection
4. Temperature and Humidity Monitoring
Frequently Asked Questions from Texas Homeowners
Q: Do garage floor coatings really perform differently in Texas than in other states?
Q: Can I install a quality coating system myself to save money?
Q: How soon can I use my garage after coating installation?
Q: What about outdoor surfaces like driveways and patios?
Texas weather is in a league of its own. From scorching triple-digit summer days to unexpected freezes, torrential spring rains to months-long droughts, our climate throws challenges at home surfaces that folks in other states simply don't face. And perhaps no surface in your home takes this punishment more directly than your garage floor.
As a DFW-based garage flooring company that's installed hundreds of floors across North Texas, we've seen firsthand how different coating systems perform in our unique climate. The truth is, a garage floor coating that works beautifully in Michigan or California might fail miserably in Texas conditions.
So what exactly makes Texas weather so challenging for garage floors, and which coating system stands up best to our particular brand of meteorological mayhem? Let's break it down with some straight Texas talk.
Why Texas Weather Creates Unique Challenges for Garage Floors
Before diving into specific coatings, it helps to understand exactly what makes our Texas climate so tough on garage floors:
The Brutal Summer Heat Factor
Those 100°+ summer days don't just make us cranky—they're murder on garage floors too:
Concrete Expansion: Extreme heat causes concrete slabs to expand, putting stress on rigid coating systems.
Hot Tire Pickup: When tires bake on asphalt in summer heat and then park on your coated garage floor, they can reach temperatures of 150°+ where they contact your floor. This heat can literally reactivate the adhesive in lesser coatings, causing the coating to stick to your tires and peel away—a phenomenon called "hot tire pickup."
Accelerated Curing Issues: DIY epoxy kits applied during Texas summers often fail prematurely because the extreme heat accelerates chemical reactions during curing, preventing proper bond formation.
The Moisture and Humidity Challenge
From Houston's famous humidity to DFW's spring storms, moisture creates serious issues:
Vapor Transmission: Many Texas homes are built on slabs without proper vapor barriers. When moisture rises through concrete (a process called hydrostatic pressure), it can push coatings right off the surface.
Condensation Cycles: The dramatic temperature swings between our air-conditioned homes and outdoor heat create perfect conditions for condensation to form on garage floors, which can delaminate improperly installed coatings.
Flash Flooding Concerns: Many Texas neighborhoods have experienced flooding, which can seep into garages and devastate lesser floor coatings.
The Expanding Soil Reality
If you've lived in Texas long enough, you've probably noticed cracks in your driveway or foundation. That's our expansive clay soil at work:
Concrete Movement: As soil expands and contracts with moisture changes, concrete slabs shift, creating stress that can crack rigid coating systems.
Slab Deflection: Significant soil movement can cause subtle dips or rises in your garage floor over time, breaking the bond of inflexible coatings.
Joint Movement: Control joints in concrete (those straight lines cut into your garage slab) allow for movement, but create weak points where poor-quality coatings often fail first.
The UV Intensity Issue
Texas sees roughly 35% more sunny days than the national average, with particularly intense UV radiation:
Yellowing Acceleration: Standard epoxy coatings yellow dramatically faster in Texas garages than in northern states, especially near doors where sunlight enters.
Degradation of Resins: UV exposure breaks down the chemical bonds in coating resins, causing premature breakdown of overall coating integrity.
Color Fading: Decorative chip systems with poor UV resistance can lose their vibrant appearance in just a couple of years in Texas garages.
Comparing Popular Garage Floor Coatings in Texas Conditions
With these challenges in mind, let's evaluate how the most common garage floor coatings perform specifically in Texas weather:
1. DIY Epoxy Kits (The Texas Test Failure)
Average Performance in Texas: 6-18 months before significant issues develop
Common Texas-Specific Failures:
Hot tire pickup during first summer
Delamination during spring humidity cycles
Severe yellowing within first year
Cracking along control joints during soil movement cycles
Texas Reality Check: While these affordable big-box store kits might perform acceptably in milder climates, they're simply not engineered for Texas extremes. We've replaced hundreds of failed DIY floors across DFW, often within a year of homeowner installation.
2. Professional Standard Epoxy Systems (The Compromise Option)
Average Performance in Texas: 2-4 years before requiring maintenance or replacement
Texas Performance Notes:
Better hot tire resistance than DIY kits but still vulnerable during extreme heat waves
Improved adhesion but still prone to eventual failure from concrete movement
Yellowing occurs more slowly but becomes noticeable within 2-3 years in sunny garages
Good chemical resistance against oil drips and automotive fluids
Texas Reality Check: Professional epoxy systems cost less than premium options and outperform DIY kits significantly. For budget-conscious Texas homeowners or those planning to move within 2-3 years, a professional epoxy installation offers a reasonable middle ground.
3. Polyurea Coating Systems (The Texas Weather Champion)
Average Performance in Texas: 10-15+ years with minimal maintenance
Why Polyurea Excels in Texas Conditions:
Thermal Flexibility: Remains pliable between -60°F to 180°F, allowing it to expand and contract with Texas concrete movement
UV Stability: Resists yellowing even with direct sunlight exposure through garage doors
Superior Hot Tire Resistance: Maintains integrity even when Texas summer heat bakes tires to extreme temperatures
Rapid Cure Technology: Most installations complete in one day with same-day or next-day use, meaning less vulnerability during unpredictable Texas weather
Moisture Tolerance: Better resistance to vapor transmission issues common in Texas slabs
Impact Resilience: Maintains integrity when tools or heavy objects are dropped, common in busy Texas family garages
Texas Reality Check: While polyurea systems typically cost 15-30% more than standard epoxy initially, their substantially longer lifespan in Texas conditions makes them the most economical choice for homeowners planning to enjoy their homes for more than a few years.
4. Hybrid Polyaspartic Systems (The Speed Champion)
Average Performance in Texas: 8-12+ years with proper maintenance
Texas Performance Highlights:
Extremely rapid cure time (beneficial during Texas humidity windows)
Excellent UV resistance comparable to polyurea
Very good hot tire pickup resistance
Can be applied in wider temperature ranges than epoxy (helpful during Texas's unpredictable weather windows)
Texas Reality Check: Polyaspartic systems offer many benefits similar to polyurea with sometimes even faster installation times, making them excellent for Texas garage conditions. However, some formulations can be less flexible than pure polyurea, which can be a disadvantage with Texas's soil movement issues.
5. Tile Systems (The Modular Option)
Average Performance in Texas: 7-10+ years depending on type and installation
Texas Performance Factors:
No chemical bond with concrete means no delamination issues during moisture or heat cycles
Drainage options helpful during Texas flash flooding events
Individual tiles can be replaced if damaged
Expansion capacity built into modular design helps with concrete movement
Texas Reality Check: While not a coating per se, interlocking garage tiles offer an alternative that addresses some Texas-specific challenges. However, they can trap moisture underneath in high-humidity areas, and some styles create noise when driving over them. They're worth considering for specific situations but aren't typically our first recommendation for most Texas homes.
The Clear Winner for Texas Garages: Polyurea Coating Systems
After installing thousands of garage floors across Texas over the years, we've found polyurea coating systems to be the clear performance leader in our challenging climate. Here's why they consistently outperform alternatives specifically in Texas conditions:
1. Formulated for Extreme Conditions
Modern polyurea systems were originally developed for industrial environments far more demanding than residential garages. This industrial heritage gives them a substantial durability advantage in handling Texas weather extremes.
2. Flexibility Matches Texas Soil Reality
The molecular structure of polyurea creates a coating that remains flexible even when fully cured. This flexibility is crucial in Texas, where soil movement is a fact of life. While rigid epoxy cracks when concrete shifts, polyurea flexes with the movement, maintaining its integrity.
3. Rapid Installation Reduces Weather Variables
Texas weather can change dramatically in hours. Polyurea's quick cure time means most installations complete in a single day, dramatically reducing the chance of weather interference during the critical curing period. Most homeowners can park on their new floors within 24 hours, compared to 5-7 days with epoxy systems.
4. Superior Heat Resistance for Texas Summers
With excellent temperature resistance up to 180°F, polyurea easily handles the hot tire issues that plague Texas garages during summer. The chemical bonds remain stable even when tires reach temperatures that would reactivate adhesion in lesser coatings.
5. Lifespan Economics Make Sense
While the initial investment in a polyurea system runs higher than basic alternatives, the extended lifespan dramatically reduces the lifetime cost. A polyurea floor typically costs $5.00-$6.00 per square foot in Texas but lasts 10-15+ years. Compare this to reapplying a budget coating every 2-3 years, and the economic advantage becomes clear.
Real Texas Customer Examples: Coating Performance in Action
Nothing demonstrates performance like real-world examples from fellow Texans:
The North Dallas Hot Tire Test
A North Dallas customer had previously installed a DIY epoxy kit that failed spectacularly during the first summer, with tire lanes peeling up after just two months. We installed a polyurea system in 2017, and despite their black Tesla sitting in the same parking spots through multiple 100°+ summers, the floor shows zero signs of hot tire pickup.
The Southlake Soil Movement Challenge
A customer in Southlake had experienced three failed epoxy installations (two DIY, one professional) that all cracked along with their shifting foundation. After installing our polyurea system in 2016, they've experienced additional foundation movement—yet the garage floor remains intact without cracks thanks to the coating's flexibility.
The Houston Humidity Test
A Houston-area customer with severe moisture issues had experienced "bubbling" with two previous coatings due to vapor transmission. After proper moisture testing and the installation of a specialized polyurea system with enhanced moisture mitigation in 2018, their floor has remained adhered despite Houston's famous humidity.
How to Choose the Right System for Your Texas Garage
While polyurea is the performance champion in Texas conditions, the right system for your specific situation depends on several factors:
Consider Your Time Horizon
Selling within 2 years: A professional epoxy system might be adequate and save on upfront costs
Staying 5+ years: Polyurea's long-term value and performance make it the clear choice
Forever home: Invest in a premium polyurea system with maximum build thickness and warranty coverage
Evaluate Your Garage Usage
Daily family use with multiple vehicles: Polyurea's durability shines in high-traffic environments
Rarely used secondary garage: You might be able to get by with a less premium system
Workshop or gym use: Consider enhanced texturing for slip resistance with polyurea
Assess Your Concrete Condition
New construction: Any quality system can perform well on virgin concrete
Older slabs with minor issues: Polyurea's flexibility accommodates imperfections better
Significant moisture problems: Specialized moisture mitigation systems may be needed before any coating
Factor in Your Local Microclimate
Texas microclimates create different priorities:
Gulf Coast (Houston area): Prioritize moisture resistance and humidity tolerance
North Texas (DFW area): Focus on soil movement accommodation and hot tire resistance
West Texas: UV stability becomes even more critical in these high-sun environments
South Texas: Heat resistance is paramount in areas seeing the most 100°+ days
Why Professional Installation Matters Even More in Texas
While professional installation is important anywhere, Texas conditions make it absolutely critical. Here's why:
1. Proper Moisture Testing
Professional installers conduct calcium chloride or relative humidity testing to measure moisture vapor transmission—a particular concern in many Texas slabs. DIY installers typically skip this critical step.
2. Diamond Grinding vs. Acid Etching
Diamond grinding creates a mechanical bond profile that withstands Texas heat cycles far better than the chemical etching used in DIY applications. Professional diamond grinding opens the concrete pores properly for maximum adhesion.
3. Texas-Specific Product Selection
Professional installers customize their systems for specific Texas conditions. For example, we might use different formulations for a west-facing garage in Plano versus a shaded garage in Lakewood, based on sun exposure.
4. Temperature and Humidity Monitoring
Professionals monitor conditions during installation and adjust processes accordingly—critical during Texas weather swings. They understand the dew point calculations that determine whether conditions are suitable for coating application.
Frequently Asked Questions from Texas Homeowners
Q: Do garage floor coatings really perform differently in Texas than in other states?
A: Absolutely. The combination of extreme heat, high UV exposure, and active soil movement creates challenges that many coating systems simply aren't engineered to handle. Systems that perform adequately in northern states frequently fail prematurely in Texas conditions.
Q: Can I install a quality coating system myself to save money?
A: While DIY installation is possible, the failure rate in Texas is exceptionally high due to our challenging conditions. The surface preparation requirements, moisture testing, and product formulation knowledge become even more critical here. Most DIY installations in Texas show significant issues within the first year.
Q: How soon can I use my garage after coating installation?
A: With polyurea systems, you can typically park on your new floor within 24 hours of installation. Traditional epoxy systems generally require 5-7 days of cure time before vehicle traffic, which means parking outside during unpredictable Texas weather.
Q: What about outdoor surfaces like driveways and patios?
A: Exterior concrete surfaces face even greater challenges in Texas weather. While some coating systems can be modified for outdoor use, completely exposed surfaces typically require specialized exterior-grade products with enhanced UV protection and different application methods.
Q: How do the costs compare to national averages?
A: Garage floor coating costs in Texas typically run slightly higher than national averages due to the specialized formulations required for our climate. However, the cost difference is minimal compared to the performance benefits of systems engineered for our conditions.
Conclusion: Making the Right Choice for Your Texas Garage
When it comes to garage floor coatings in the Lone Star State, not all systems are created equal. Our challenging climate demands solutions specifically engineered to handle extreme heat, intense UV exposure, unpredictable moisture, and active soil movement.
After years of installing and monitoring different coating systems throughout Texas, polyurea clearly emerges as the best performer in our unique conditions. Its flexibility, UV stability, rapid installation, and exceptional hot tire resistance make it ideally suited to tackle everything Texas weather throws at it.
While the initial investment runs higher than budget alternatives, the extended lifespan and reduced maintenance make polyurea the most economical choice for Texas homeowners planning to enjoy their homes for more than a few years. When you factor in the convenience of one-day installation and same-day or next-day use, the value proposition becomes even stronger.
At VistaPro Garage Coatings, we believe in being transparent about how different systems perform in real-world Texas conditions. We offer both polyurea and epoxy options and are happy to provide honest guidance about which makes the most sense for your specific situation, budget, and local microclimate.
Ready to transform your garage floor with a coating system engineered for Texas weather? Contact us for a free, no-pressure consultation and quote. Our Texas-based experts understand our unique climate challenges and will help you choose a solution that stands up to everything the Lone Star State throws at it.